OKM Co., Ltd. General machinery and toolsFactory-ONE MF
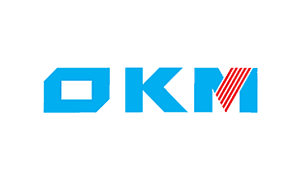
Founded in 1902 as a manufacturer of working tools specialized mainly in valve production, OKM has been working on cutting-edge product development since 1952, based on "creating products that please our customers." The company provides high-performance, high-quality and high-reliability valves to various fields such as air conditioning equipment, chemical industry, steel industry, shipbuilding, petroleum, desalination plants, food industry, government offices, etc.
Background of the implementation of the new system
Before introducing the current system, the company was using general-purpose platform for salary, sales, purchasing, and financial management system developed internally. Regarding manufacturing management, only inventory and backlog management functions were in operation. Since the system were developed by the company internally, it was customized based on the requests of the departments that would use the system. As a result, the system expanded excessively and the data was decentralized, resulting in an inconsistent, so-called spineless system.
While continuing to operate the system that had become inefficient as described above, in 2004, the top management decided to:
1) Build a core system that could respond to future increases in sales with a small number of people
2) Eliminate the inefficiency through centralizing the scattered data
3) Implementation of manufacturing management system that would enable visualization of inventory, lead time shortening, and cost grasping.
A new system concept was launched based on these requirements. In order not to repeat the failure of the previous management system, OKM started to actively search for the suitable system.
System selection criteria
When it comes to the new system, the company consulted with their management consultant. They were adviced to proceed with system construction based on the manufacturing management system. Then, OKM chose a SI vendor that builds the system in scrap&build way and also chose two manufacturing management packages. There were concerns about whether it is a good idea to build a new system from zero considering the previous experience. Ultimately, they decided to:
1) Build a core system based on a manufacturing management package with a solid core.
2) Improve internal business processes through using the core system to improve efficiency further.
Based on decisions mentioned above, the company researched a lot of packages including packages introduced by management consultants and packages of other companies and eventually, Factory-ONE hybrid edition that can handle both MTO production and repetitive production was chosen. The main deciding factors for going ahead with Factory-ONE was the fact that the basic functions met OKM’s requirements, and above all, it was possible to customize the system in-house (open source).
Since the company originally developed the system in-house, they wanted to use the package for the core functions and then develop the branches by themselves considering costs. In that sense, open source was a great advantage when selecting a system. Thus, it was decided that the next system would be built with the Factory-ONE as the core system, and the project started.
Challenges when implementing the new system
Several months have passed since the kick-off of the implementation, and in March 2006, the customization program was completed and master registration was started, but the system implementation was extremely challenging due to two major factors. The first factor was the start-up project of the Chinese factory, which was running at the same time with the new system implementation project. Since the launch of the Chinese factory was a top priority project that was expected to bear the fate of the company in the future, organizational changes were made, and some of the main members of the system replacement project were assigned to the factory launch project, so the system replacement project started off with fewer members than planned. With the small number of project members left, we managed to register the master, helped the staff understand the new system and acquire operational skills, and we also provided education and guidance to the field workers. However, due to lack of labor, education and guidance did not fully cover all field workers.
The second was parallel operation of the old system. Since the parallel operation was carried out in a state where education and guidance could not be thoroughly conducted for all members, it was not possible to switch operations well at the site, and there were also cases of double data registration, so the implementation of the new system was dragging on. Although some functions were operating, they were in a state that was far from the original purpose and expectations of implementation.
In the long run, Chinese factory launch was settled down and the new system implementation project that had been dragging on was restarted. The first thing that was done when restarting was to clarify the gap between the goals set at the beginning of implementation and the current situation, identify the problems that led to the project to drag on, and consider countermeasures. As a result, we decided to increase the number of project members by three and rebuild the operation system. The three staff members thoroughly learned and understood the Factory-ONE, and then shared the knowledge acquired with the actual work site. Moreover, instead of simply providing operational education and guidance, we kept providing guidance and education until everyone gained an understanding of the significance of the new system for the company and employees.
As a result of the steady activities of such dedicated staff, the accuracy of master registration improved after half a year, and the understanding of the new system in the field as well as awareness towards the importance of the new system increased significantly. Then, in July 2007, we were able to integrate the operations of the old system into a new system.
Benefits of implementation
1) Sales have increased significantly compared to previous years and in addition the system can be operated without the need in additional staff because the efficiency of handling administrative tasks has been greatly improved.
2) The new system enabled data centralization.
3) Inventory waste was reduced by understanding the inventory state, and due to the many useful functions such as MRP calculation, export of various documents, etc. a significant reduction in lead time was achieved.
4) The company managed to understand cost generation much better than before.
After all, so-called visualization was a big benefit, allowing the company to able to see the state of internal processes within the factory in numbers, tables, graphs, etc.
Main products
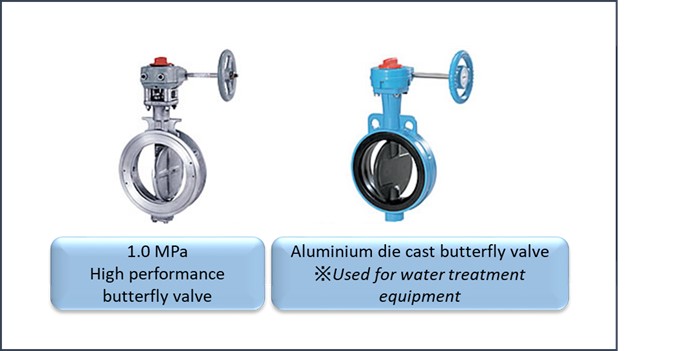