Sales Order, Shipping
Manage planned orders (planned production numbers) based on sales order information and sales order status. Manage backlog, manage effective inventory and actual inventory associated with inventory allocation& withdrawal, arranging delivery, checking delivery date change history, and warn of delivery delays. Multi-item one-leaf format. It is also possible to import the confirmed order information sent by EDI from the customer into the production order. The shipping process can be performed through linking to the order information (shipping without receiving an order is possible). Installment payment and cancellation options are available as well. In addition, it is possible to omit the sales data entry by shipping in "shipping = sales mode".
Production planning
Manage planned orders (planned production numbers) based on sales order information and sales order status. Manage backlog, manage effective inventory and actual inventory associated with inventory allocation& withdrawal, arranging delivery, checking delivery date change history, and warn of delivery delays. Multi-item one-leaf format. It is also possible to import the confirmed order information sent by EDI from the customer into the production order. The shipping process can be performed through linking to the order information (shipping without receiving an order is possible). Installment payment and cancellation options are available as well. In addition, it is possible to omit the sales data entry by shipping in "shipping = sales mode".
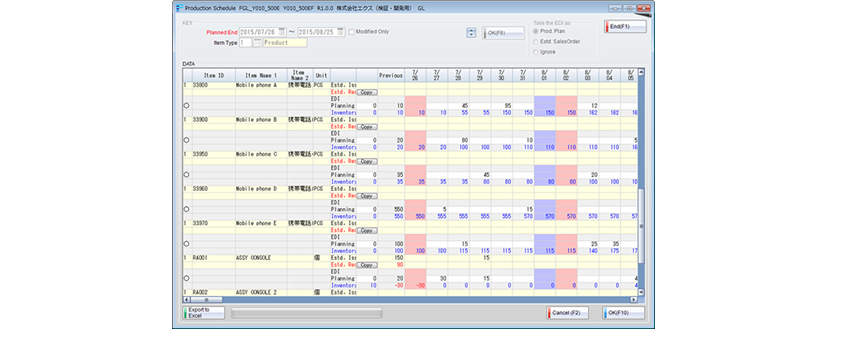
Materials requirement planning (MRP)
Performs calculation of materials required for production (MRP processing) based on the created standard production plan. Based on the item composition master (hierarchical bill of materials * tree structure), performs "summarizing", "rounding", etc. for the net required material quantity obtained by subtracting the inventory reserves from the total required material quantity for each level, and creates the order schedule data. In addition, process arrangements (manufacturing instructions) are performed in parallel with material arrangements (purchase), and based on the standard process plan and purchase lead time, order dates (starting date) and delivery dates (completion date) are calculated (Lead time offset). Calculate (lead time offset). Since repeated calculation is available until settlement processing is performed, you can also simulate material order planning as well as workload planning.
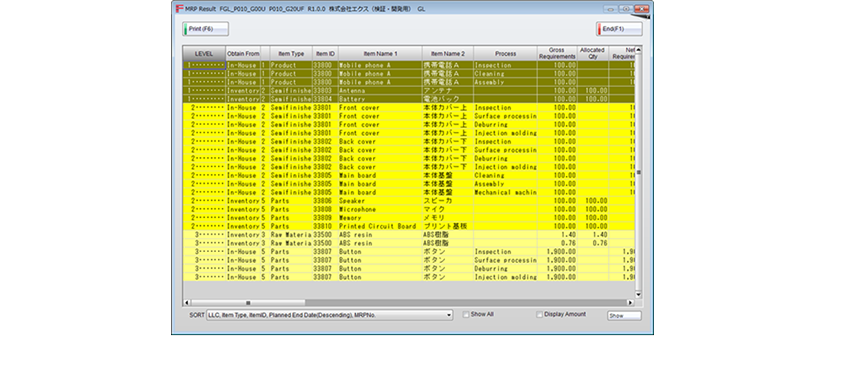
Progress
You can compare and view work instructions and fulfillments in Gantt chart format. In the case of material requirements calculation (MRP processing), you can inquire through the multi-stage expanded image of master menu, and in the case of production work order, you can inquire through the work schedule image from the order information.
Workload adjustment
Calculate the workload factor per day by comparing the man-hours owned (fixed man-hours + adjusted man-hours) for each arrangement destination and machine, and the workload man-hours calculated from the standard man-hours (arrangements&work) of the indicated remaining man-hours and standard information. Workload factor is displayed in various colors depending on workload level. It is also possible to display the retained man-hours and the workload man-hours as a graph.
Purchase order, receipt
Generates order placement information of material purchase& outsourcing request by confirming the arrangement information. In the case of material requirements calculation (MRP processing), process instructions& orders within the company are treated as orders, similarly as in the case of outsourcing requests. It is possible to automatically select the supplier with the lowest price. You can manage order data from multiple perspectives, such as managing the order backlog and checking the delivery date change history. In the receiving process, you can enter the receipt of purchased products and outsourced processed products and the volume in the in-house process. By making the purchase order form a slip with a barcode for each item, it is possible to save labor in receiving work. You can also receive multiple orders at once (through specifying the supplier, serial number, etc.). Installment payment and cancellation options are available as well. It is also possible to omit the purchase entry by accepting in "receiving = stocking mode".
Inventory
With inventory inquiry, you can search actual inventory and effective inventory from multiple perspectives, including search by product number, location, one-stage& multi-stage development (parent-child relationship), and receipt / payment details (plan and actual). Entry / exit is linked with each system such as receipt and shipping entry. In the receiving process, if the parent item is received, the previous process or the child item is issued at the same time. In addition, we also perform "presumed delivery" based on theoretical values on standard information, and withdrawal of actual values by manual entry. Factory-One also supports supply management, inventory batch return, inventory adjustment, inventory transfer, inventory count, etc..
Lot tracking function ※Optional
Enable lot traceability by registering the lot number for each entry (receiving, work fullfillment, request fullfillment, shipping). Traceability information is displayed in a tree structure format, and it can handle both forward expanding from product to material and reverse expanding from material to product.
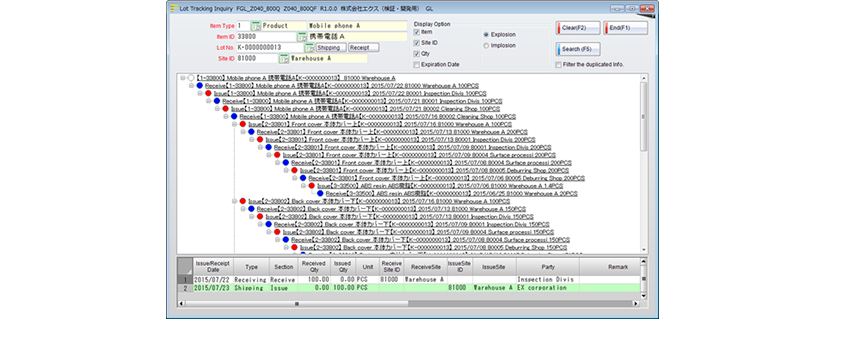