TAIYO AQURIS CO, LTD.Metal products<Factory-ONE MF (MRP)
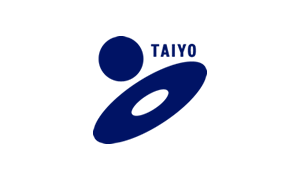
Taiyo Aquris is an electronic components manufacturer that handles operations from mold design and manufacturing to press working. It was founded in April 2007 after Electrical Engineering Division was spun off from Taiyo Kikai Kogyo Co., Ltd. Responding to just-in-time ahead of other companies within the same industry, a flexible manufacturing system was established by the company with both hard-side aspects such as compound processing lines through using press technology and progressive cold forging lines, and soft-side aspects such as quality control and production management systems. Below, we will provide the background from the development-stage of the new system to its implementation.
Background of the implementation of the new system
In May 2006, the company started developing a new manufacturing management system with a development vendor in order to switch from mass production type which no longer met the needs of the times to high-mix low-volume production as well as to change the old sales management system which was also obsolete. However, shortly after starting the system design, Taiyo Aquris had to suspend it.
The first cause of the suspension was the in-house project system. We selected project members based on their knowledge and proficiency in PC, but it eventually turned out that those who were familiar well with the daily business operations didn’t have the right to make decisions, and managers who had the right to make decisions were not familiar well with the daily business operations. Second, the development vendor the company was working with didn’t have enough know-how related to the manufacturing industry. Since there were too many requirements needed to be met in the new system related to various parts of the business operations and production, eventually the vendor couldn’t combine all of them into one system due to man-hours, know-how lack and complexity of the task.
After that, the new system development restarted in August 2007. In order not to repeat the experience of the past, the company started creating an in-house project system that highlighted the three points shown below:
(1) Top-down organization
(2) Selecting project team members from each department based on their skills and knowledge related to daily business operations as well as their execution power.
(3) Establishment of secretariat for promotion.
System selection criteria
Considering the costs and reduction of the development period due to the impact of the previous failure, Taiyo Aquris came up with the decision to build a new system based on package software. To help select the package, they invited an external IT advisor. Three products were being considered including Factory-ONE MF and software from other vendors.
As a result, Factoy-One MF was chosen as a new system. The main reasons were because it incorporated all the basic and required functions of the manufacturing management system such as EDI linkage and MRP functions, and since the source of the program is open to the public, it could be customized in-house, which enables cost reduction and development in a short time. At that stage, only seven months were left before it went live.
Challenges when implementing the new system
It was quite a challenging mission to implement the new system in 7 months. Therefore, in order to improve the efficiency of system development, the company promoted the project focusing on the following points.
(1) Create a business process flow based on hearings from each department, and ensure that preliminary meetings between the executive office and the person in charge of the department are held before the meeting with the vendor SE.
(2) Understand the gap between the current business process flow and the flow in Factory-ONE MF, and based on this consider the minimum customization needs. In addition, the advice received from an external IT advisor that "customization of the core part of the system should be prioritized above all" was taken into consideration as well when promoting the system development.
After many meetings with each department, customization requests were growing and the budget was nearly to be exceeded. But taking advantage of the open source program, and acquiring the skills of Crystal Report and Object Browser, the company solved the problem by dealing with the various forms and tables creation in-house.
In this way, the new business process flow and new system design document were completed in December 2007. It was quite a long way and a lot of work up to that point, but fortunately, thanks to the members who were familiar well with the work and who had the ability to execute tasks, we were able to complete it successfully.
After the new system design document was approved and customization process started off, the following tasks was carried out in order in the project:
(1) Master registration and maintenance
(2) Creation of an operation manuals
(3) Operation guidance to the person in charge of data entry
(4) Pilot tryout
(5) Go-live
In this project, the period from pilot tryout to the rollout (so called “go live”) was particularly challenging. Even though the company wanted to spend two months on the pilot tryout stage, due to the suspension and negative impacts of the previous system development, we had to implement the new system in only two weeks. Moreover, there were frequent input delays due to lack of proficiency in system operations, and more. In the long run, it was decided to rollout the system despite some Master defects. Even after rollout, input delays occurred frequently. This affected the credibility of the data and made it difficult to manage them. Insufficient preparation for pilot tryout hindered the switching off the old and new systems after go-live which eventually led to extension of the parallel operation period by one month.
The maintenance of the old system was finished at the end of April 2008, and after that no further schedule extension was allowed. Therefore, we thoroughly examined the mechanism that causes input delay. Then, as a result of all the staff as well as the project team members working together to solve various issues that was hindering the smooth operation, there was record-breaking increase in orders in April 2008. And despite the fact that the workload on the site had reached it’s limit, one month later, the company was able to completely switch the systems in May.
Benefits of implementation
When using the old system, it would usually take about 8 hours for production planning and arranging materials. Now, with Factory-ONE the same tasks are performed in 40 minutes. In addition, there is no need for rich expertise and knowledge, so even a newcomer can easily perform these duties. Also in inventory management of the previous system,
(1) The inventory of the previous day couldn’t be grasped until noon of the following day.
(2) It wasn’t possible to keep track of the inventory movements to the outsource destination.
Not only these problems have been solved, but it also became possible to inquire about materials, work in process, finished products, and moving products in real time. Now, monthly inventory count is no longer different from actual inventory, and inventory loss has been reduced greatly. In addition, the on-time delivery rate has been improved from 60% to 100%, and finally the company was able to improve operations and efficiency.
Main products:
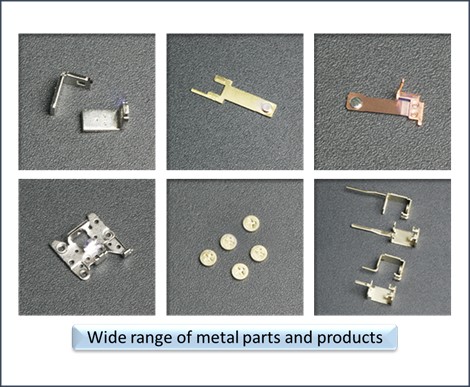